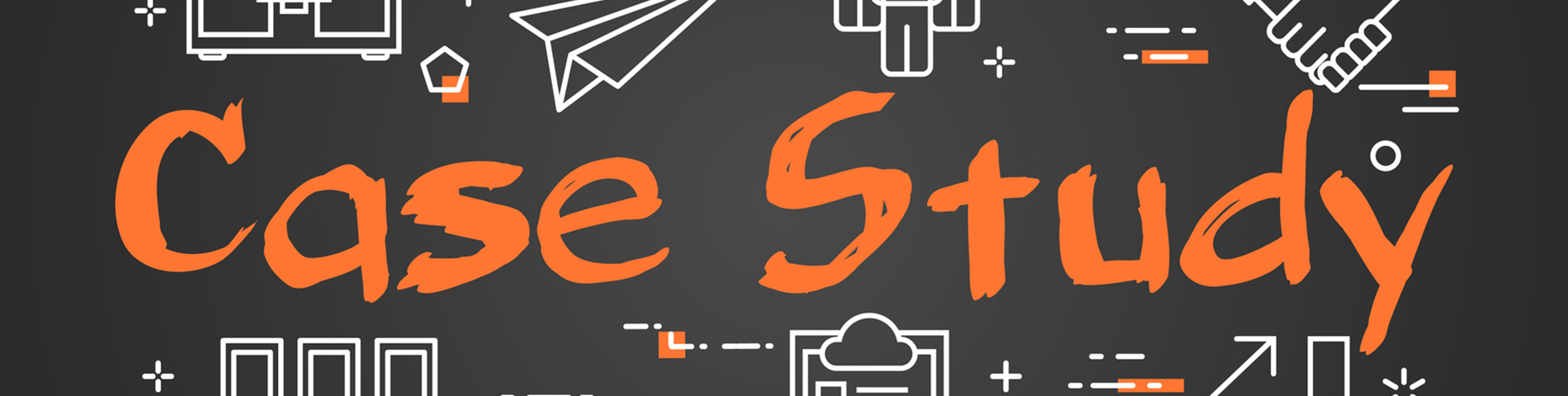
BODYSHOP Express
3777 Gaines St.
San Diego CA 92110
(619) 732-6300 Office
Bodyshop Express is a Collision Repair facility fully certified to repair the vehicles on the road today. In our information sheet you can see our certifications and Insurers that we do business for. But what you do not see is what the purpose and intention of why Bodyshop Express was built.
I have been in the collision business for over 35 years and after selling my eight-store chain that I owned with my partners I still felt that the industry needed to change for the better. It was a constant struggle to deliver consistent quality product and at the same time met the ever-changing demands of the market place and the multiple customers we served. One day we were heroes for half of our customers and at the same time not doing so well for the others. This hit hard with me, as we all worked hard each and every day to service all of our customers equally. But as we all need to be at the forefront of change, we in essence were still fixing cars the way we had for years.
It was because of the battle to satisfy, that even after I sold my business I was still left with a feeling of not being satisfied with what we had accomplished, and further where the current industry was going. I came across some new technology, not new to the world but new to the US, when coupled with a process to complement the equipment it can deliver consistent performance to multiple stake holders simultaneously!
This was this reason that Bodyshop Express was built and formed, not only as a business or collision repair facility, but most importantly to demonstrate that there is now the opportunity to change the way we do business for the better. This new way of processing vehicles benefits all constituents. This has become our challenge how do we get insurers to think of us as something different, how do we get insurers to step out of the box and work with us to try something different that will benefit insurers, repairers and customers.
Just as we stepped out of our comfort zone and built a new facility and invested hundreds of thousand dollars in a market where we had never operated we ask for some faith from a few insurers to look at what we are trying to do and possibly giving us a trial of 4-6 months to demonstrate that we can do things differently and we can process cars differently with the byproduct being unique and definitely worth the investment for what it will provide in the future. What we do here today can impact our industry in the future and years to come, as stated in the industry publications every day of saved rental saves the insurers $200.000.000 million dollars a year.
What does the new equipment allow us to do? Gas Catalytic or Electric IR Curing Technology.
- Cure products base coats, clears, primers, plastics many times quicker and 100% cured.
- Process up twice as many vehicles through a paint booth in one day than conventional booths, 8-12 RO’s per day 1 booth.
- Booth Cycles 25-55 minutes versus 55 minutes to 1.45 hrs.
- Cure primers, base and clears and fillers in minutes.
- Half cycle time 4-5 days and increase TT 4-8 HPD.
This technology is not new as I stated, but it is new to the US market. Recently a company named Bodyshop Revolution North America, Symach and GFS Revo have taken the time to do what had not been done up to now, which allowed for the technology to be imported into the US market, get full ETL and UL certification. While this was being achieved BRNA also said if we can use these Technologies to do these things maybe we can also process cars completely different than in the past in order to take and achieve the most out of this new technology. So, looking at other industries and incorporating things that they did when new technology and equipment has been introduced into the market place I have incorporated and developed a process around this equipment. It also revolves around the theory of constraints as taught by Michael Goldratt. The theory of constraints concerns itself with what is it that stops production and what can we do to eliminate this and allow the process and equipment to give us the biggest benefit?
What are the differences or changes we have introduced into the collision repair facility to enable,” Continuous Work Flow”?
If we can cure products, primers, filers, plastics in minutes how will this impact change. If we can use roll priming in an open environment how can this impact change. By incorporating a rail system and robotic curing or mobile units that can be taken to a technician’s work stalls we do a number of things that create continuous work flow. With instant curing technicians only need one car at time to work on, continuously, not stop and go. By allowing roll priming and instantly curing the product you enable the technician to finish off his own work and not passing it along to someone else to finish. By roll priming we eliminate a whole department and the establishment of another que, every time we create que’s we lengthen cycle. By roll priming or spray priming with 3oz cups we do not have inosinate contamination in the workplace nor do we have overspray onto other vehicles.
Now you can think of each stall as project stall, where multiple operations can be accomplished in the same stall. What is and has always been the issue with collision repair is no two collisions are alike, or the high variability of collision repair. Consequently, multiple departments and many ques, and lengthened cycle. If each stall has the capability to fix a 50-hour repair today or a 20-hour repair tomorrow, we can handle the high variability of the different collisions. Not only do we handle variability, but we have eliminated 3 additional departments and three additional que’s. When several stalls are equipped with lifts and pull station’s they can accomplish 80-95% of all structural or pulls in a strong reliable pull station. Stations that can lift up to 9,000 lbs. and use as many as two 10-ton towers. Work stations equipped like this can take a car form measure, pull, repair, block and prime all in one stall and all while achieving continuous work flow. The only thing left to do to a vehicle now is paint prep? If we did everything else in this stall and the vehicle has been blocked and primed, why would we create another department for paint prep. As I have mentioned every time we create departments we create lines because no one is generally waiting for the next car they are working on cars, so lines back up. What we will do is finish the paint prep and pre masking in the technician’s stall. When a car goes to paint it is ready to be painted other than blow for dust, wash the panels to be painted and then bag the vehicle. What I have just explained is by using new technology and a process that allows for the fullest utilization what we achieved is continuous workflow by one technician working on one vehicle, not 2,3 and as many as 6 cars in production by one technician at a time. They can only work on one car at a time?
This process allows for the only place that a car stops, or waits is in front of the paint booth, where we want the constraint, because we want to always have a car ready when the car in the booth is done. One car rolls out and back to the technician for reassembly and another car goes into the booth. We use these technologies in the booth as well, where we can process a car from start to finish in 25-55 minutes all while achieving 70% reduction in energy. These new Curing process cure vehicles out of paint equal to a 30-day cure. Thus, vehicles can immediately be buffed and reassembled immediately out of paint. Again, even though we created a small que in front of paint after being painted we are again able to continuously work on a vehicle till it is delivered. Our goal would be two to three days faster in front of the booth and save 1-2 days after paint.
There are two other critical aspects of the process that must take place to insure continuous work flow. The first main issue is estimates, drivable, drop offs, and tow ins. We must have accurate estimates and minimal supplements to enable continuous work flow. Tow ins must have a strict and rigid blue printing process in order to determine all the parts necessary one time and one parts order. Secondly, we must determine a much better way to handle drivable estimates. What have we done in the past, many times we do a visual inspection and preorder parts and schedule the customer in based on poor pictures and an inaccurate parts order. Upon drop off we do the disassembly only to find out we have additional parts we need to order. Consequently, the car then sits out back for 2-3 days waiting for parts and waiting to go into production. Or the other situation is we say we cannot order al of the parts until we do a complete disassembly, so we bring the car in do our thing and again it sits out back for 2-3 three days. What this does is create large amounts of WHIP and definitely increases cycle in many cases unnecessarily.
We have demonstrated that on any given week 50-70% of customers that come in with a drivable hit for an estimate can be handled much differently. If we were to at that time when determined they want to use our facility for repairs to do a much better analysis of the damage we could literally get a 100% parts order. By explaining to our mutual customers that in order to process your vehicle more effectively and expeditiously if you would allow us to do a thorough inspection in one of our estimating bays we could do a couple of things. First, we could insure your car is safe to drive and any loose parts could either be secured or removed at this time. Secondly by doing a complete inspection today we could get an accurate determination of all the parts your car will require us to order. If the car is determined to be safe to drive, we would then preorder all parts and schedule the customer in for repairs when their parts are in and we have a repair slot for their car. It is our goal to put cars into production the same day they are dropped off for repairs. So, all parts at facility and car dropped and ready to be put into production. Within one hour of inserted into production any issues rather it be clips or minor repair it is determined, and the estimate is locked while technician continues to work on vehicle continuously to its completion.
- Results that we are looking to Achieve.
- Cycle times dramatically reduced consistently and for multiple insurers. 5.5 days or less all hits.
- Repair vs Replace in the 60 plus range.
- Parts reduction and severity reductions.
- Energy savings of 70% in associated repairs.
- 30-35% additional production in same facility with same number of technicians and management team.
- Reduction of in house WIP by 55% plus.
- CSI insurer and shop improved and industry leading.
- Consistent, repeatable and top of market metrics.
- Make more $$ and give better performance simultaneously to all insurers, can you achieve both, YES!!!